Finite element analysis and optimization of the structure of a machine tool
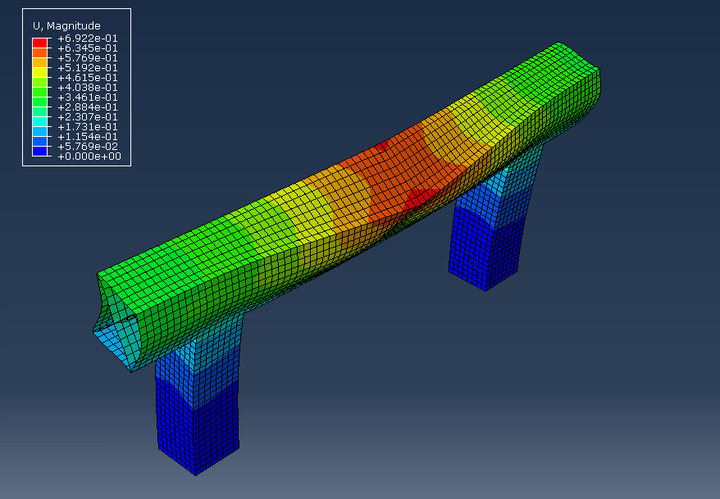
Finite element analysis and optimization of the structure of a machine tool
In this project, I analyzed the structural behavior of a machine tool system using the finite element method. I used Abaqus CAE to solve the FE problem in a 3D simplified model of the machine tool structure.
Then, I defined a sizing optimization for the cross-section of the structure to optimize the thickness and increase the first eigenfrequency by 25%. Lastly, I modified the geometry of the cross-section. The optimization process has been done on the modified cross-section to find the minimum thickness by minimizing the volume and satisfying the minimum requirements of the problem.
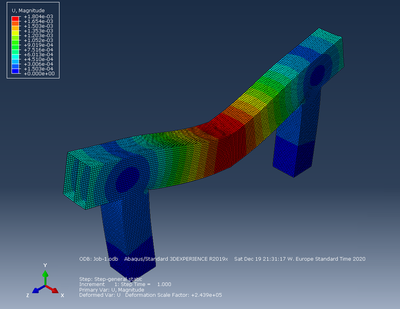
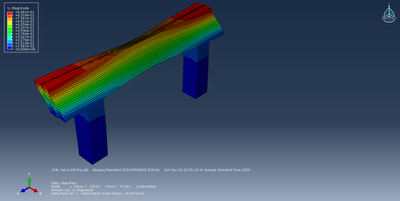
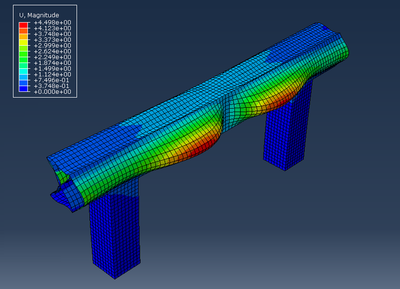